商習慣の見直しで適正在庫を保つ。物価上昇と物流課題に負けない戦略を
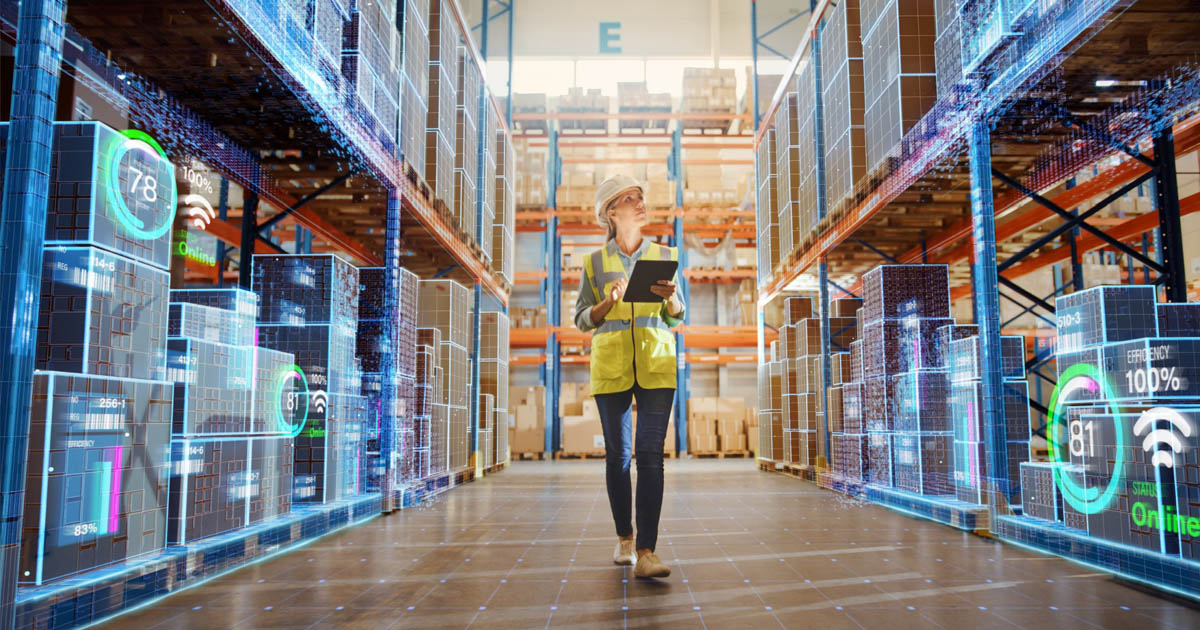
天井の見えない物価上昇と、2024年問題が迫り来る小売業にとって、どのように利益を追求するかは非常に難しい課題と言えます。
この苦境を勝ち残るために注目されているのが、在庫リスクの低減と適正在庫を保つためのシステム整備です。
欠品や過剰在庫を防いで、在庫が適正な状態を保ち続ける事が、コストを削減して利益を最大化する事につながっていきます。
本稿では、過剰在庫や不良在庫がどのようなリスクとなりうるのかを改めて検証し、その影響を記載しています。
従来の商習慣や業務プロセスを大胆に見直して、在庫を企業の資産として効率よく運用する=在庫リスクを低減する方法について紹介しながら、業界を超えた提携の可能性やDX推進で見えてくる利点についても紹介していきます。
無料メルマガ登録はこちら:ストアデジタルの今をひも解くメルマガをお届け適正在庫で在庫リスクを低減
適正在庫は、企業が利益を出すために必要な在庫量で、欠品や過剰在庫を防ぐ事で利益率を向上させ、運送費をはじめとしたコストを抑える事ができます。
適正在庫に似た言葉として「安全在庫」というワードがありますが、これは欠品を防ぐために確保したい最低数の在庫を意味する言葉です。
安全在庫数をあらかじめ設定しておけば、需要の変動があったとしても、また悪天候等で配送スケジュールが遅れたとしても対応して欠品という事態を回避する事が可能です。
安全在庫は下限のみの設定なのに対して、適正在庫は在庫数の下限と上限を定めるのが普通です。
なぜなら、適正在庫は欠品と過剰在庫の両方を防ぐ必要があるからです。
適正在庫を求める計算式は、安全係数と欠品許容率を用いて「安全在庫+サイクル在庫」という式から算出する方法以外にも、在庫回転率と期間を導いてから「安全在庫+需要数」で計算する方法があります。
また、当該在庫でどれくらい儲かっているのかを示す交叉比率を使って、適正在庫を金額から求める計算も可能です。
過剰在庫、不良在庫が経営に与える影響
在庫が適正でない状態は、過剰在庫となります。
過剰在庫は不良在庫の発生するリスクを高め、経営上の悪影響となります。
■過剰在庫
過剰在庫は、売れ行き以上に生産してしまった製品を指します。
余分に在庫があると欠品を防ぎ、需要の急増にも対応できるというメリットがあります。
一方で、在庫が多すぎると保管スペースが多く必要となり、管理費用がかさむといったデメリットがあります。
■不良在庫
長期間在庫を保管していると、在庫の品質劣化や陳腐化(製品がトレンドから外れて流行遅れになる事)を招く等、商品価値そのものが損なわれるリスクも発生します。
つまり、不良在庫とは、売れる見込みがないだけでなく、経済的な悪影響が懸念される在庫を指します。
具体的には、その在庫がある事で良質な他の在庫が劣化するリスクがあるものを意味しています。
不動在庫や低回転在庫、死に筋在庫と呼ばれる事もあります。
在庫の消化が利益増加に直結するとは限らない
余剰在庫や不良在庫は、最終的に廉価販売や廃棄によって消化されます。
廉価販売や廃棄は、それだけで利益を損なうアクションですが、それに伴う作業とコストも見過ごせない存在と言えるでしょう。
廉価販売や廃棄にまつわる作業やコストは、かからないに越したことはありません。不良在庫の解消に、わざわざ本来かける必要のない手間とコストをかけてまで、利益率を下げる行為をしている事になるからです。
こうした在庫や販売手法(あるいは廃棄)を減らす事は、全体的な利益を増やすためにも有効です。
適正な在庫数を知って、その数字を保つ事が利益の最大化につながっていきます。
廃棄ロスを防ぎ適正在庫で運営するメリット
不良在庫は、売れない在庫としてずっと保管しておくのにコストがかかり、廃棄するのにもコストがかかるため、なるべく出さないようにするのが得策です。
廃棄ロスを防ぐメリットは、大きく分けて3つあります。
最も大きなメリットはコストカットでしょう。
適正在庫で運営すれば保管スペースや管理費用も適正に抑えられるため、不要なコストはかかりません。余剰在庫が多いと別に倉庫を借りたり作業スタッフを雇用したりする必要が生じるので、余計なコストや作業が発生してしまいます。
また、在庫の質が損なわれて不良在庫になれば廃棄にも多額の費用がかかります。
不良在庫を出さない事が、利益を最大化する事につながります。
第二に重視すべきメリットは、商品価値を保てるという点です。
余剰在庫が多くなれば在庫を減らすために値引き販売をしなければならなくなるかもしれません。
値下げしないという事はそれだけで大きな商品価値となります。
三つめは、経営全体の視点でのメリット「キャッシュフローの改善」が挙げられます。
在庫は棚卸資産で、企業の資産と見なす事ができます。
在庫が動かないと自由に使える資金が増えません。資本の固定化、すなわち在庫が商品ではなく在庫であり続ける限り、資金繰りを圧迫してしまいます。
在庫を適正に保つ事でキャッシュフローをスムーズにする事ができるはずです。
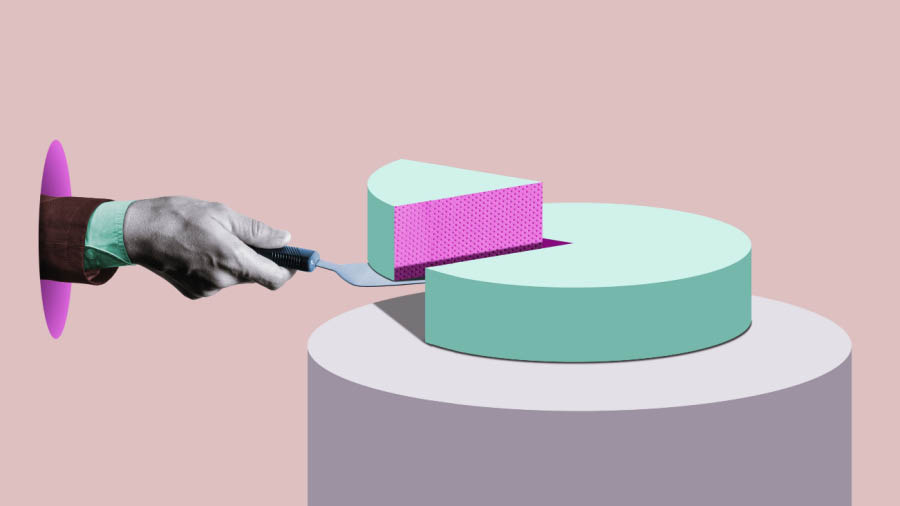
商習慣、ビジネスプロセスの見直し
適正在庫のためには、在庫管理の見直しだけでなく、時に商習慣やビジネスプロセスそのものを根本的に見直す必要があります。
これまで当たり前とされてきた風潮を大胆に改革する、業界の枠にとらわれずに協業体制を築いて互いの強みを活かした新たなプロセスを構築するといった戦略が在庫を適正に保つ鍵を握る事もあります。
家電メーカーの取り組み
家電業界の製品は、これまで発売してから半年程経過すると、2割程度値引きして販売されていました。
そして、この値崩れを取り戻すためにマイナーチェンジを繰り返してきました。
この負のサイクルを変えるために家電メーカーが打ち出したのが、量販店に対する「価格指定」です。
従来の家電は、量販店等の小売側が店頭価格を決めていました。
価格指定は、家電メーカーが販売価格を決定するため、小売店は自分たちで店頭価格や在庫処分価格の設定をできなくなります。
その代わりに、店舗からの返品を受けつけて小売店の在庫リスクを低減する措置を取る事になっています。小売店は値引きができない代わりに、売れ残りの返品を行う事で利益を守れるという仕組みです。
店頭価格がメーカー据え置きになると、メーカーは利益を守る事ができます。
しかし、消費者の選ぶ目はシビアになるでしょう。そこで功を奏してくるとメーカーが考えるのが、繰り返されるマイナーチェンジを止める事です。マイナーチェンジが常態化していると、それだけ一つの製品にかける開発時間は短くなり「そこそこ」の製品があふれてしまう可能性があります。
これを止める事で、充分な開発時間を確保し、消費者のニーズに合致する製品を作り出そうというのがメーカーのビジョンです。
この実現のために、ある家電メーカーは量販店と在庫数を共有するシステムを試験的に導入しました。リアルタイムで売れ筋や在庫の残りを把握して、需要に対する過不足ない在庫製造、価格づけを行う事ができると期待されています。
アップサイクルを取り入れるアパレル企業
創造的再利用と日本語に訳される「アップサイクル」を取り入れる事で適正在庫を保つ施策が、アパレル業界でスタートしています。
リサイクルというと一度使ったものや廃棄されたものを、再利用するイメージですが、アップサイクルは本来捨てられるはずの製品、すなわちまだ廃棄はされていないが近いうちに廃棄されてしまうものを、製品として生まれ変わらせる手法を意味します。
例えば、廃棄予定の余剰デニムを使ったファッション小物や、複数枚の衣服の傷んでいない部分をつなぎ合わせて作った新しいジャケット等がアップサイクルされたアパレルアイテムに該当します。
この他、アパレルでは1着から注文できる受注生産型の販売モデルも展開していて、在庫リスクを限りなくゼロに近づける計画が推進されています。
業界を超えた連携
製品の出荷から輸送、小売店到着までをリアルタイムで一元管理できれば、余剰在庫や欠品、輸送中のミスによる破損からの在庫廃棄といった無駄を極限まで減らせる可能性が高まります。
家電メーカーが小売店と在庫数をリアルタイムで共有するような連携が、これからはさらに求められていくでしょう。
ゆえに、小売と製造だけでなく、そこへIT業界も加わった包括的な連携も視野に入れていくのがこれからの企業の生存戦略となります。
物流業界では、厳格な温度管理が求められるケースの多い医薬品分野から、順次ブロックチェーン技術の活用が始まっています。
ブロックチェーンは、日本語で「分散型台帳」と訳される情報管理技術です。ネットワークに参加している複数の企業・業者が取引履歴等を共有できる上、改ざんリスクが低いのが特徴です。
複数の企業が協業体制をとる際、こうした安全で便利な情報共有技術は欠かせません。
24時間の厳格な品質管理が求められる医薬品を筆頭に、衝撃や振動で傷みが生じるリスクのある農産物や、偽物撲滅を掲げるブランド品等をブロックチェーンで管理していく事が期待されています。
小売業、製造業、IT業とでは、ビジネスプロセスはそれぞれ異なりますが、DX化とビジネスプロセスの改善を行う事で、業界の垣根を超えた事業展開が見えやすくなり、自社の業界における優位性を確立しやすくなるでしょう。
在庫と物流の課題も
在庫の問題解決は、物流の課題解決にも直結しています。
2024年問題で運べなくなる荷物は、10%とも30%とも言われていますが、対策を講じているのは一部の運送会社のみで、人手不足により具体的な策を講じる余力がないという企業が多いのが実情です。
もともと他の業種と比較すると賃金が低い傾向にあるとされる運送業ですが、残業時間が制限されれば、さらに手取りが減って転職や離職が加速する懸念もあります。
大手自動車メーカーは物流会社に支払う料金を上げて、残業が減っても賃金が減らないような仕組みを整え、一部地域で運送のスタイルを変更するといった対策をとっています。
輸送をトラックではなく鉄道・船舶に切り替えるモーダルシフトを実施する企業も少しずつ出てきましたが、現時点ではトラック輸送よりも鉄道の方がコストが高いとあって、大々的な導入には至っていません。
政府は、「物流革新緊急パッケージ」として共同輸送の促進、自動フォークリフトの導入といった策を打ち出していますが、2025年には14万人ものドライバーが不足するという見通しも出ています。
日本経済全体の特徴として、各企業ともにサプライチェーン(供給網)戦略を重視して、物流戦略を疎かにしてきたという実情があります。
在庫リスクを減らすためには、少量の配送を何度も繰り返すのが原則でしたが、2024年問題を目前にしてこの考え方は改める必要があるかもしれません。
物価上昇にも影響
こうした施策にかかるコストは、製品価格に転嫁されます。
日本商工会議所によると、多くの中小企業は、エネルギー価格の高騰、最低賃金の上昇、人手不足の深刻化、さらにインボイス制度への対応といった諸要件が重なった事で、業況が悪化している傾向にあり、物価上昇の買い控えもあって苦しい状況に置かれているとされています。
2024年問題に端を発する物流への対応についても、かかったコストは価格への転嫁が必至となるでしょう。
しかし、物価の上昇に賃金が追いついていない事から、価格を上げると顧客離れが進む懸念もあります。
発注者との価格協議については、製造業及び卸売業は高い水準で「協議できている」と考える企業が多いのに対して、小売業とサービス業は特に小規模企業で充分な協議ができていないと考える企業が多数いる事が分かっています。
これは、日本の全体的な傾向であるため、一企業が無理に価格を抑えようとするのは現実的ではないでしょう。
適正在庫のためのシステム整備を進める事で、価格転嫁以外でも利益を上げられるかもしれません。
